Electronic Components
Comtech Electronic Components Group is a leading global value-added supplier for high-reliability electrical, electronic, and electromechanical (EEE) parts and services to spacecraft and launch vehicle manufacturers and their subcontractors. Comtech bridges the gap between current parts and mission requirements with upgraded or upscreened parts or with custom-specified parts. We can also serve as your component engineering organization. We are compliant with all ITAR, EAR, and other export control regulations, and we can provide additional capacity or surge capability.
Supply Chain Management and Component Engineering
Comtech can simplify your supply chain by managing all aspects of parts procurement, component engineering and quality assurance. We lower your total supply chain costs by buying smart, reducing transaction cycles and internal touch points, managing difficult parts vendors, reducing delivery times and solving tough engineering/quality problems so you don't have to!
We are dedicated to high reliability spacecraft parts procurement and we are able to provide EEE parts from 95% of the world’s space level parts manufacturers. Our long-standing supplier relationships and experience working with manufacturers to resolve manufacturer test and quality problems is unparalleled in this industry.
Comtech is AS 9100D & ISO 9001 CERTIFIED
Radiation Components & Engineering
Think your design will work in space, just because it works on the ground? Unfortunately, the radiation environment in space is much different to that on the ground. Let Comtech help you to understand the risks involved.
In the early design phases of a program, we assist our customers with mission radiation studies, derating requirements, and recommendations for parts and materials. We work with our customers to achieve a program that meets their needs for reliability, performance, and budget. As the detail design progresses, Comtech makes specific recommendations for part, material, and process changes.
We have access to numerous radiation test facilities, so they are available when you need them and Comtech manages the testing. Our radiation test report database contains over 1000 radiation test reports. We also have access to radiation test reports from JPL, GSFC, NASA, NGST, Aerospace Corp, Sandia and many manufacturer databases.
Test capabilities include:
- Total Ionizing Dose (TID)
- Enhanced Low Dose Rate Sensitivity (ELDRS)
- Displacement Damage
- Flash X-Ray
- Electromagnetic pulse (EMP)
- SEE-Single Event Effects
- Heavy Ion testing
- Proton, neutron testing, and gamma testing
Obsolescence Management
Heritage designs are often plagued by obsolete devices and technologies. It is expensive for integrators to redesign their systems, but eventually many of the parts designed into a system become unavailable.
Don't let an obsolete part, obsolete your mission
Comtech provides the expertise to eliminate or minimize the impact of obsolescence on your design. We review your bill of materials and determine items that are approaching manufacturer end of life (EOL). We also locate alternate devices for obsolete items and provide the necessary screening to insure your high reliability application requirements are met.
Our Obsolescence Management program includes may areas of support:
- Identify and document available tools and techniques for predicting obsolescence engineering
- Research, compare, and benchmark various approaches to EEE parts obsolescence
- Research and document data on decapsulate and repackaging companies and approaches as well as their procedures to maintain product reliability & quality assurance
- Knowledge of predictive tools and methodologies comparison will aid EEE parts obsolescence evaluation for your projects
- Improvement of maintenance, reliability schedule costs, and sustaining engineering
- Extensive network of facilities that are licensed and authorized by manufacturers to provide a continuing manufacturing source for mature/discontinued product
- Potential EEE parts obsolescence candidates’ database form ISS, SSP, and OSP
Counterfeit Parts Detection
The counterfeit market is big business. According to recent reports from both government and industry, the volume of counterfeit parts in the supply chain is increasing and the counterfeiters are only getting better at what they do. Comtech’s staff are active on the on the JEDEC G-11 and G-12 component committees and SAE G-19 Counterfeit Electronic Parts Committee, to ensure that we are keeping up with the bad guys.
Comtech inspectors trained to IDEA-STD-1010-B and certified to IDEA-ICE-3000 can perform the analysis appropriate for a given lot of parts, depending on risk factors such as source and provenance. Any subset of the listed testing can be performed to ascertain with the highest level of confidence that a part is genuine. All testing performed is in accordance with current SAE standards.
- Visual inspection
- X-ray (see if samples match internally or even have a die)
- X-ray fluorescence (XRF)
- C-mode scanning acoustic microscopy (C-SAM)
- Electrical testing: Continuity, functional, DC, AC, block testing
- Destructive physical analysis to the die level, to check mask identifiers
- Basic inspection and lot homogeneity inspection
- Fourier-transform infrared spectrometry (FTIR)
- Cross-sectioning
- Other nondestructive options
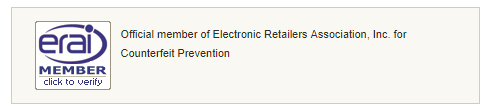
Customer Source Inspection
Since the 1970s, Comtech SCT engineers—then as part of TRW Components International—have been visiting manufacturer plant sites across America and beyond to inspect devices prior to seal and prior to shipment. With many device types, the best way to be assured of the quality of a device is to inspect it not only when its manufacture is complete, but before it is sealed. We avoid countless problems by inspecting parts during precap source inspection—performed before a device is sealed or encapsulated—or during final source inspection—performed on a completed product before it is shipped. This is done on 100% of the parts in a lot, to minimize the possibility of “escapes.”
Our engineers perform their source inspections per the requirements of MIL-STD-750 Method 2071 or JESD22-B101B but we can also tailor our inspections to any custom requirements. All required rework, causes for part or lot rejection, and other findings are documented in detail on a Quality Field Report form.